Problemas en la inyección de plásticos y cómo evitarlos
En las fábricas de inyección de termoplásticos como la nuestra, el trabajo no está exento de puntos críticos en su recorrido. En este post explicamos cuáles son algunos problemas frecuentes que podrían afectar a la calidad final de la pieza de plástico producida.
Problemas en la inyeccion de termoplasticos y cómo evitarlos
Una de las ventajas principales del uso de piezas de plástico en medicina es su relativo bajo coste en comparación con otros materiales, como el vidrio y los metales. Eso permite que los productos fabricados en plástico a menudo puedan ser del tipo monouso, siendo eliminados tras cada uso, mejorando así la seguridad.
El plástico también puede ser configurado en moldes mucho más detallados de los que se utilizan para el vidrio y los metales. Esto permite fabricar piezas complejas si es necesario que realicen funciones específicas.
Asimismo, las piezas y productos de plástico no se rompen con facilidad, por lo que ofrecen mucha flexibilidad y resistencia a la vez. Las resinas más comunes que se emplean en las piezas de plástico para el sector de la medicina son el PVC, polietileno, polipropileno y poliestireno. Aunque otros materiales (ABS, policarbonatos o poliuretanos) también están encontrando aplicaciones especializadas que requieren un alto rendimiento.
Asegure la calidad de sus piezas fabricadas
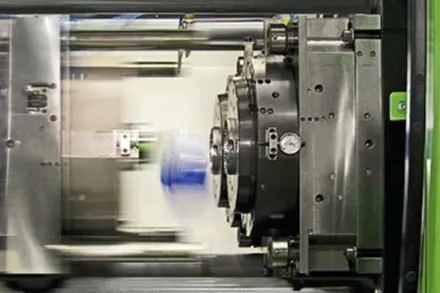